Budowa maszyn pneumatycznych opiera się na kilku kluczowych elementach, które są niezbędne do ich prawidłowego działania. W pierwszej kolejności warto zwrócić uwagę na kompresor, który jest sercem całego systemu. Jego zadaniem jest sprężanie powietrza, co pozwala na uzyskanie odpowiedniego ciśnienia potrzebnego do pracy maszyny. Kolejnym istotnym elementem jest zbiornik powietrza, który gromadzi sprężone powietrze i zapewnia jego stałą dostępność w systemie. Również ważne są zawory, które kontrolują przepływ powietrza oraz kierunek jego ruchu. Dzięki nim możliwe jest precyzyjne sterowanie pracą maszyny. Nie można zapomnieć o siłownikach pneumatycznych, które przekształcają energię sprężonego powietrza w ruch mechaniczny. Ostatnim, ale nie mniej istotnym elementem są przewody i złącza, które łączą wszystkie te komponenty, umożliwiając efektywne przesyłanie powietrza w systemie.
Jakie zastosowania mają maszyny pneumatyczne w przemyśle
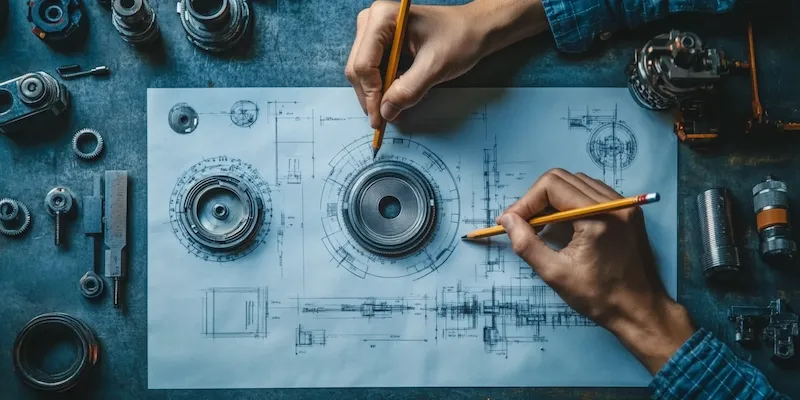
Maszyny pneumatyczne znajdują szerokie zastosowanie w różnych gałęziach przemysłu, co czyni je niezwykle wszechstronnymi narzędziami. W przemyśle motoryzacyjnym wykorzystywane są do montażu i demontażu części, co znacznie przyspiesza proces produkcji. W branży spożywczej maszyny pneumatyczne służą do pakowania produktów oraz transportu materiałów sypkich, takich jak mąka czy cukier. W przemyśle elektronicznym wykorzystuje się je do precyzyjnego montażu podzespołów oraz testowania urządzeń. Ponadto, maszyny te znajdują zastosowanie w budownictwie, gdzie używane są do podnoszenia ciężkich materiałów oraz wiertnictwa. Ich zaletą jest możliwość pracy w trudnych warunkach, gdzie inne maszyny mogą zawodzić.
Jakie są zalety i wady maszyn pneumatycznych
Maszyny pneumatyczne mają wiele zalet, które przyciągają uwagę przedsiębiorców oraz inżynierów. Przede wszystkim charakteryzują się dużą niezawodnością oraz prostotą obsługi. Dzięki nim możliwe jest osiągnięcie wysokiej wydajności produkcji przy stosunkowo niskich kosztach eksploatacji. Sprężone powietrze jako medium robocze jest łatwo dostępne i nie wymaga skomplikowanej infrastruktury do przechowywania. Dodatkowo maszyny te są bezpieczne dla środowiska, ponieważ nie emitują szkodliwych substancji chemicznych. Niemniej jednak istnieją również pewne wady związane z ich użytkowaniem. Wydajność maszyn pneumatycznych może być ograniczona przez straty ciśnienia w systemie oraz konieczność regularnej konserwacji komponentów takich jak filtry czy smarownice. Ponadto sprężone powietrze może być kosztowne w produkcji, co wpływa na ogólne koszty operacyjne przedsiębiorstwa.
Jakie nowinki technologiczne dotyczą budowy maszyn pneumatycznych
W ostatnich latach branża maszyn pneumatycznych przeżywa dynamiczny rozwój dzięki nowinkom technologicznym, które znacząco poprawiają ich funkcjonalność i efektywność. Jednym z najważniejszych trendów jest automatyzacja procesów związanych z obsługą maszyn pneumatycznych. Dzięki zastosowaniu zaawansowanych systemów sterowania możliwe jest precyzyjne monitorowanie i regulowanie parametrów pracy maszyn, co przekłada się na zwiększenie wydajności produkcji. Kolejnym innowacyjnym rozwiązaniem są inteligentne czujniki, które umożliwiają zbieranie danych o pracy maszyny oraz jej stanie technicznym. Te informacje mogą być wykorzystywane do prognozowania awarii oraz optymalizacji procesów produkcyjnych. Dodatkowo rozwijają się technologie związane z materiałami używanymi do budowy komponentów maszyn pneumatycznych, co wpływa na ich trwałość i odporność na uszkodzenia mechaniczne.
Jakie są najczęstsze problemy związane z maszynami pneumatycznymi
Maszyny pneumatyczne, mimo swoich licznych zalet, mogą napotykać różne problemy, które mogą wpływać na ich wydajność oraz niezawodność. Jednym z najczęściej występujących problemów jest wyciek sprężonego powietrza, który może prowadzić do znacznych strat energii oraz obniżenia efektywności pracy maszyny. Wyciek ten może być spowodowany uszkodzeniem przewodów, nieszczelnymi złączami lub zużytymi uszczelkami. Kolejnym istotnym problemem jest niewłaściwe ciśnienie robocze, które może wynikać z nieprawidłowego ustawienia kompresora lub awarii w systemie regulacji ciśnienia. Niewłaściwe ciśnienie może prowadzić do niewłaściwego działania siłowników oraz innych komponentów maszyny. Dodatkowo, zanieczyszczenia w sprężonym powietrzu, takie jak wilgoć czy cząstki stałe, mogą powodować uszkodzenia elementów wewnętrznych oraz obniżać jakość produkcji. Regularna konserwacja oraz stosowanie odpowiednich filtrów i separatorów mogą pomóc w minimalizacji tych problemów.
Jakie są różnice między maszynami pneumatycznymi a hydraulicznymi
Maszyny pneumatyczne i hydrauliczne to dwa różne typy systemów mechanicznych, które mają swoje unikalne cechy i zastosowania. Główna różnica między nimi polega na medium roboczym – maszyny pneumatyczne wykorzystują sprężone powietrze, podczas gdy maszyny hydrauliczne działają na zasadzie cieczy hydraulicznej. Dzięki temu maszyny hydrauliczne są w stanie generować znacznie większe siły przy mniejszych rozmiarach komponentów. Z tego powodu często znajdują zastosowanie w branżach wymagających dużej mocy, takich jak budownictwo czy przemysł ciężki. Z kolei maszyny pneumatyczne są bardziej odpowiednie do aplikacji wymagających szybkiego ruchu i precyzyjnego sterowania, co czyni je idealnymi do montażu i pakowania. Kolejną różnicą jest sposób działania – maszyny pneumatyczne są zazwyczaj lżejsze i łatwiejsze w utrzymaniu, ale ich wydajność może być ograniczona przez straty ciśnienia. Maszyny hydrauliczne natomiast wymagają bardziej skomplikowanej infrastruktury i regularnej konserwacji, ale oferują większą moc i stabilność.
Jakie są przyszłościowe kierunki rozwoju technologii maszyn pneumatycznych
Przyszłość technologii maszyn pneumatycznych rysuje się w jasnych barwach dzięki ciągłemu postępowi technologicznemu oraz rosnącemu zapotrzebowaniu na efektywne rozwiązania przemysłowe. Jednym z kluczowych kierunków rozwoju jest integracja sztucznej inteligencji oraz uczenia maszynowego w procesach zarządzania i monitorowania pracy maszyn pneumatycznych. Dzięki tym technologiom możliwe będzie przewidywanie awarii oraz optymalizacja procesów produkcyjnych w czasie rzeczywistym. Kolejnym ważnym trendem jest rozwój materiałów kompozytowych i lekkich stopów metali, które mogą znacząco zwiększyć efektywność energetyczną maszyn oraz ich trwałość. Również automatyzacja procesów produkcyjnych staje się coraz bardziej powszechna, co pozwala na zwiększenie wydajności oraz redukcję kosztów operacyjnych. Warto również zwrócić uwagę na rosnącą rolę zrównoważonego rozwoju i ekologicznych rozwiązań w projektowaniu maszyn pneumatycznych, co może wpłynąć na zmniejszenie ich wpływu na środowisko naturalne.
Jakie są podstawowe zasady bezpieczeństwa przy pracy z maszynami pneumatycznymi
Bezpieczeństwo pracy z maszynami pneumatycznymi jest kluczowym aspektem, który należy uwzględnić na każdym etapie użytkowania tych urządzeń. Przede wszystkim pracownicy powinni być odpowiednio przeszkoleni w zakresie obsługi maszyn oraz zasad BHP związanych z ich użytkowaniem. Ważne jest również regularne przeprowadzanie przeglądów technicznych oraz konserwacji sprzętu, aby zapewnić jego sprawność oraz uniknąć potencjalnych awarii. Należy także stosować odpowiednie środki ochrony osobistej, takie jak gogle ochronne, rękawice czy kaski, aby zminimalizować ryzyko urazów podczas pracy. Kolejnym istotnym aspektem jest kontrola ciśnienia roboczego – należy upewnić się, że nie przekracza ono dopuszczalnych wartości określonych przez producenta maszyny. W przypadku wystąpienia jakichkolwiek nieprawidłowości lub usterek należy natychmiast przerwać pracę maszyny i zgłosić problem odpowiednim służbom technicznym.
Jakie są koszty eksploatacji maszyn pneumatycznych
Koszty eksploatacji maszyn pneumatycznych mogą się znacznie różnić w zależności od wielu czynników, takich jak rodzaj zastosowania, skala produkcji czy specyfika używanych komponentów. W pierwszej kolejności warto zwrócić uwagę na koszty związane z energią potrzebną do sprężania powietrza – im większa wydajność maszyny, tym więcej energii będzie potrzebne do jej prawidłowego działania. Koszty te mogą być znaczne, zwłaszcza jeśli system nie jest odpowiednio zoptymalizowany pod kątem efektywności energetycznej. Kolejnym istotnym elementem kosztowym są wydatki związane z konserwacją i serwisowaniem sprzętu – regularne przeglądy techniczne oraz wymiana zużytych części są niezbędne dla zapewnienia długotrwałej sprawności maszyn pneumatycznych. Dodatkowo warto uwzględnić koszty materiałów eksploatacyjnych, takich jak filtry czy smary, które również wpływają na ogólny bilans kosztów eksploatacji.
Jakie są najlepsze praktyki przy projektowaniu systemu maszyn pneumatycznych
Projektowanie systemu maszyn pneumatycznych wymaga uwzględnienia wielu czynników, które mają wpływ na jego efektywność oraz niezawodność. Przede wszystkim kluczowe jest dokładne określenie wymagań dotyczących wydajności oraz specyfiki zastosowania danego systemu. Należy również zadbać o odpowiedni dobór komponentów – każdy element powinien być dostosowany do pozostałych części układu, aby zapewnić optymalną współpracę całego systemu. Ważnym aspektem jest także ergonomia – projektując stanowiska pracy należy uwzględnić komfort operatorów oraz łatwość obsługi urządzeń. Kolejną istotną praktyką jest stosowanie nowoczesnych technologii monitorowania i zarządzania pracą systemu – dzięki temu możliwe będzie szybkie reagowanie na ewentualne problemy oraz optymalizacja procesów produkcyjnych.