Destylator przemysłowy to urządzenie, które odgrywa kluczową rolę w wielu procesach produkcyjnych, zwłaszcza w przemyśle chemicznym, petrochemicznym oraz spożywczym. Jego głównym zadaniem jest oddzielanie składników cieczy na podstawie różnic w temperaturze wrzenia. Proces ten polega na podgrzewaniu mieszaniny, co powoduje odparowanie substancji o niższej temperaturze wrzenia, a następnie skraplaniu pary w celu uzyskania czystego produktu. W przemyśle chemicznym destylatory są wykorzystywane do produkcji różnych chemikaliów, takich jak alkohole, kwasy czy oleje. W przemyśle spożywczym natomiast destylatory służą do produkcji napojów alkoholowych, takich jak whisky czy wódka, gdzie kluczowe jest uzyskanie wysokiej czystości trunku. Warto również wspomnieć o zastosowaniach destylatorów w przemyśle naftowym, gdzie służą do separacji różnych frakcji ropy naftowej, co pozwala na uzyskanie paliw oraz innych produktów naftowych.
Jakie są rodzaje destylatorów przemysłowych i ich cechy
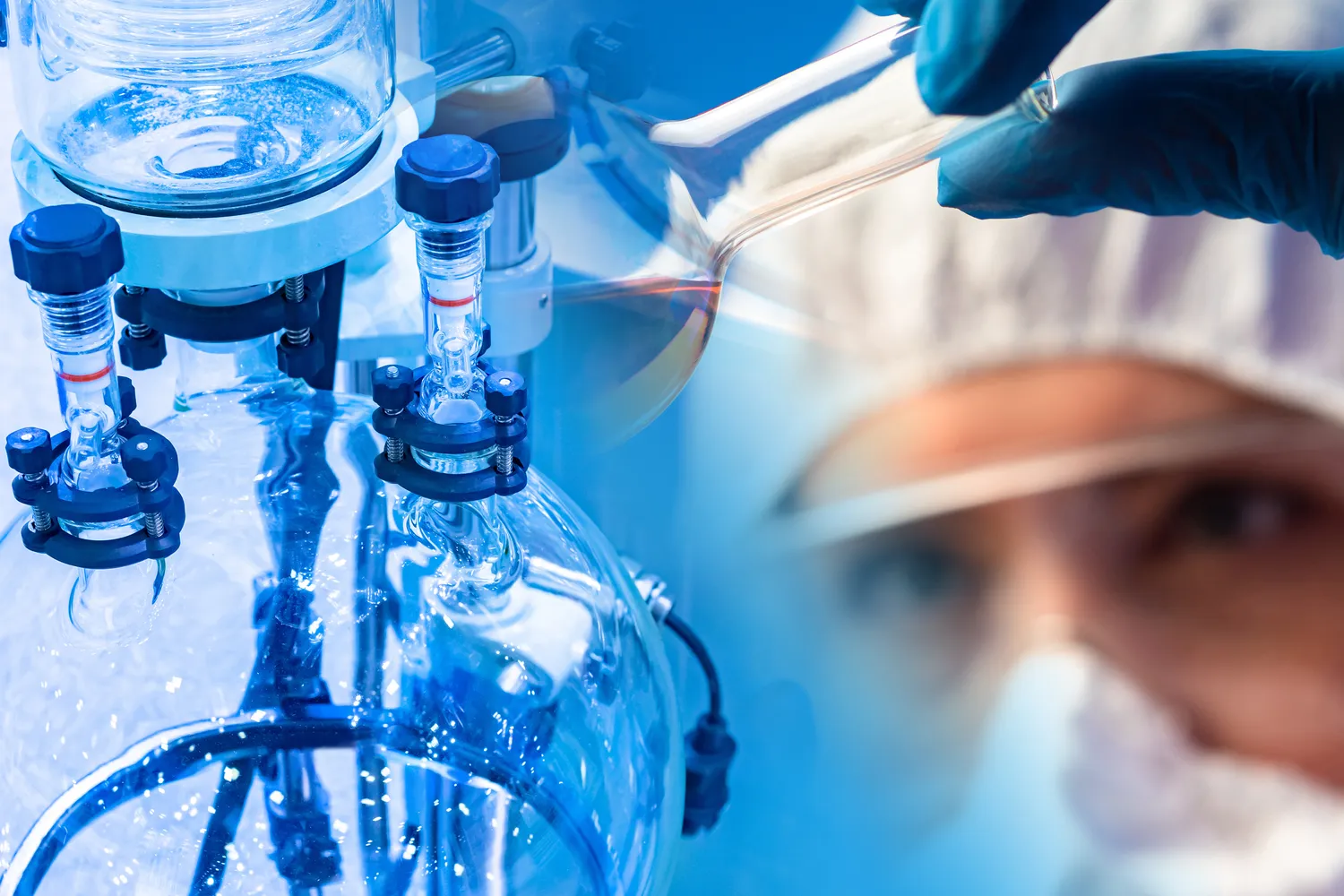
Wśród różnych typów destylatorów przemysłowych można wyróżnić kilka podstawowych kategorii, które różnią się konstrukcją oraz zastosowaniem. Najpopularniejszym rodzajem jest destylator prosty, który składa się z jednego kolumny i jest stosunkowo łatwy w obsłudze. Umożliwia on separację składników o znacznej różnicy temperatur wrzenia. Kolejnym typem jest destylator frakcyjny, który wyposażony jest w kolumnę frakcyjną i pozwala na bardziej precyzyjne oddzielanie składników o zbliżonych temperaturach wrzenia. Tego rodzaju destylatory są szczególnie przydatne w przemyśle petrochemicznym oraz chemicznym. Istnieją także destylatory próżniowe, które działają w obniżonym ciśnieniu, co pozwala na destylację substancji w niższych temperaturach, minimalizując ryzyko degradacji termicznej. Dodatkowo można spotkać destylatory azeotropowe, które umożliwiają oddzielanie składników tworzących azeotropy, czyli mieszaniny o stałym składzie.
Jakie są zalety stosowania destylatorów przemysłowych w produkcji
Stosowanie destylatorów przemysłowych niesie ze sobą wiele korzyści dla producentów w różnych branżach. Przede wszystkim pozwalają one na uzyskanie wysokiej czystości produktów końcowych, co jest kluczowe dla jakości wyrobów chemicznych oraz spożywczych. Dzięki efektywnemu oddzielaniu składników możliwe jest zminimalizowanie zanieczyszczeń oraz poprawa stabilności chemicznej produktów. Kolejną zaletą jest możliwość optymalizacji procesów produkcyjnych poprzez zwiększenie wydajności i redukcję kosztów operacyjnych. Nowoczesne destylatory są często wyposażone w zaawansowane systemy automatyzacji oraz monitoringu, co pozwala na bieżące śledzenie parametrów pracy i szybką reakcję na ewentualne nieprawidłowości. Dodatkowo stosowanie destylatorów przyczynia się do ochrony środowiska poprzez zmniejszenie ilości odpadów oraz emisji szkodliwych substancji do atmosfery.
Jakie są najnowsze technologie stosowane w destylatorach przemysłowych
W ostatnich latach nastąpił znaczący rozwój technologii związanych z destylacją przemysłową, co przyczyniło się do zwiększenia efektywności oraz oszczędności energetycznych tych procesów. Jednym z najnowszych trendów jest zastosowanie technologii membranowej, która pozwala na separację składników bez konieczności podgrzewania ich do wysokich temperatur. Dzięki temu można uniknąć degradacji termicznej substancji oraz zmniejszyć zużycie energii. Innym innowacyjnym rozwiązaniem są systemy hybrydowe łączące tradycyjne metody destylacji z nowoczesnymi technologiami separacyjnymi takimi jak ekstrakcja czy adsorpcja. Tego rodzaju podejście umożliwia jeszcze dokładniejsze oddzielanie składników oraz poprawę jakości produktów końcowych. Warto również zwrócić uwagę na rozwój inteligentnych systemów zarządzania procesami destylacyjnymi opartych na sztucznej inteligencji i uczeniu maszynowym. Takie rozwiązania pozwalają na optymalizację parametrów pracy urządzeń w czasie rzeczywistym oraz przewidywanie ewentualnych problemów zanim one wystąpią.
Jakie są wyzwania związane z eksploatacją destylatorów przemysłowych
Mimo licznych zalet, eksploatacja destylatorów przemysłowych wiąże się z pewnymi wyzwaniami, które mogą wpływać na efektywność procesów produkcyjnych. Jednym z głównych problemów jest konieczność regularnego czyszczenia i konserwacji urządzeń. Z czasem w destylatorach mogą gromadzić się osady oraz zanieczyszczenia, które mogą obniżać wydajność i jakość destylacji. Dlatego ważne jest, aby zakłady przemysłowe wdrażały odpowiednie procedury utrzymania ruchu, co wiąże się z dodatkowymi kosztami oraz przestojami w produkcji. Kolejnym wyzwaniem jest zarządzanie zużyciem energii. Destylacja jest procesem energochłonnym, a rosnące ceny energii mogą znacząco wpłynąć na koszty operacyjne. W związku z tym wiele firm poszukuje sposobów na optymalizację zużycia energii poprzez zastosowanie nowoczesnych technologii oraz odzyskiwanie ciepła. Dodatkowo, zmieniające się regulacje dotyczące ochrony środowiska stawiają przed producentami nowe wymagania dotyczące emisji i odpadów, co może wymagać dostosowania istniejących systemów destylacyjnych do nowych norm.
Jakie są kluczowe komponenty destylatora przemysłowego
Destylator przemysłowy składa się z kilku kluczowych komponentów, które współpracują ze sobą w celu efektywnego przeprowadzenia procesu destylacji. Podstawowym elementem jest zbiornik na ciecz, który umożliwia podgrzewanie mieszaniny do odpowiedniej temperatury. Zbiornik ten często wyposażony jest w system grzewczy, który może być oparty na parze wodnej, elektryczności lub innym źródle ciepła. Kolejnym istotnym elementem jest kolumna destylacyjna, która pełni rolę miejsca separacji składników. Wewnątrz kolumny znajdują się różne elementy takie jak talerze czy wypełnienia, które zwiększają powierzchnię kontaktu między parą a cieczą, co sprzyja efektywnemu oddzielaniu składników. Po przejściu przez kolumnę para trafia do skraplacza, gdzie następuje jej kondensacja i powrót do stanu ciekłego. Skraplacz może być chłodzony wodą lub innymi czynnikami chłodzącymi. Dodatkowo ważnym komponentem jest system kontroli i monitoringu, który pozwala na bieżące śledzenie parametrów pracy destylatora oraz automatyczne dostosowywanie ustawień w celu optymalizacji procesu.
Jakie są różnice między destylatorami przemysłowymi a laboratoryjnymi
Destylatory przemysłowe i laboratoryjne różnią się przede wszystkim skalą produkcji oraz zastosowaniem. Destylatory przemysłowe są zaprojektowane do pracy w dużych zakładach produkcyjnych i mają na celu przetwarzanie dużych ilości surowców w krótkim czasie. Ich konstrukcja jest zazwyczaj bardziej skomplikowana i wyposażona w zaawansowane systemy automatyzacji oraz monitoringu, co pozwala na efektywne zarządzanie procesem destylacji na dużą skalę. Z kolei destylatory laboratoryjne są mniejsze i służą głównie do przeprowadzania eksperymentów oraz badań naukowych. Ich budowa jest prostsza, a obsługa często wymaga większej interwencji ze strony operatora. W laboratoriach często stosuje się destylatory prostsze w konstrukcji, takie jak destylatory kulowe czy prostokątne, które pozwalają na łatwe oddzielanie składników w niewielkich ilościach.
Jakie są przyszłościowe kierunki rozwoju technologii destylacyjnej
Przemysł destylacyjny stoi przed wieloma wyzwaniami związanymi z rosnącymi wymaganiami dotyczącymi efektywności energetycznej oraz ochrony środowiska. W związku z tym przyszłość technologii destylacyjnej będzie koncentrować się na innowacjach mających na celu poprawę wydajności procesów oraz redukcję negatywnego wpływu na środowisko naturalne. Jednym z kluczowych kierunków rozwoju będzie dalsze doskonalenie technologii odzyskiwania ciepła, co pozwoli na zmniejszenie zużycia energii podczas procesu destylacji. Dodatkowo coraz większą rolę będą odgrywać technologie oparte na sztucznej inteligencji i uczeniu maszynowym, które umożliwią optymalizację procesów w czasie rzeczywistym oraz przewidywanie ewentualnych problemów zanim one wystąpią. Warto również zauważyć rosnące zainteresowanie alternatywnymi metodami separacji substancji chemicznych, takimi jak ekstrakcja cieczy czy chromatografia, które mogą stanowić uzupełnienie tradycyjnych metod destylacyjnych. Ponadto rozwój materiałów o wysokiej wydajności oraz nanotechnologii może przyczynić się do stworzenia bardziej efektywnych systemów separacyjnych.
Jakie są przykłady zastosowań destylatorów przemysłowych w różnych branżach
Destylatory przemysłowe znajdują szerokie zastosowanie w różnych branżach gospodarki, co świadczy o ich wszechstronności i znaczeniu dla wielu procesów produkcyjnych. W przemyśle chemicznym służą do produkcji różnych substancji chemicznych takich jak alkohole etylowe czy kwasy organiczne, które są wykorzystywane jako surowce do dalszej obróbki lub jako składniki produktów końcowych. W przemyśle petrochemicznym destylatory odgrywają kluczową rolę w procesie rafinacji ropy naftowej, gdzie umożliwiają oddzielanie różnych frakcji paliwowych oraz innych produktów naftowych takich jak oleje czy smary. W branży spożywczej natomiast stosowane są do produkcji napojów alkoholowych takich jak whisky czy gin, gdzie istotne jest uzyskanie wysokiej jakości trunku o odpowiednich właściwościach organoleptycznych. Destylatory znajdują również zastosowanie w przemyśle farmaceutycznym do produkcji substancji czynnych leków oraz ich oczyszczania. Dodatkowo coraz częściej wykorzystywane są w sektorze biotechnologicznym do separacji białek czy enzymów z kultur komórkowych.